The future of manufacturing depends on unifying your entire industrial ecosystem, bridging IT and OT to enable smarter, faster, and more secure operations. As Industry 4.0 continues to reshape the industrial landscape, IT/OT convergence is no longer optional. It’s mission-critical.
By 2025, over 75% of leading manufacturers will have implemented some form of convergence between IT and OT networks, driving up to 20% gains in operational efficiency. This isn’t hypothetical. IIoT (industrial internet of things) platforms, OT devices, and industrial control systems (ICS) are now tightly integrated with scalable data analytics engines, enterprise IT systems, and cybersecurity frameworks.
Modern manufacturers face increasing disruptions across their supply chains, heightened pressure on business operations, and growing OT security threats targeting legacy workflows and critical infrastructure. The convergence of IT with OT departments empowers leaders to streamline operations, unlock actionable operational data, and deploy new technologies across industrial environments faster without sacrificing resilience or uptime.
In this guide, we’ll explore why IT convergence is essential for modern industrial automation, reveal high-impact use cases from across the sector, and detail how unified strategies protect your OT cybersecurity posture while enabling enterprise-wide transformation. You’ll also discover how Keystone delivers the expertise to help you secure, optimize, and scale your convergence journey across every layer of your technology stack.
Key Takeaways
- IT/OT convergence lets you connect your entire industrial environment for smarter, more efficient operations.
- Real-time data from OT devices fuels faster, more accurate decisions that boost output and reduce waste.
- Predictive maintenance and integrated quality control lower downtime and improve product reliability.
- You gain stronger OT security and simplified compliance through unified cybersecurity strategies.
- Choosing the right partner, like Keystone, helps you scale your technology stack with confidence and precision.
Why Unifying IT and OT Matters
Manufacturers today face a new mandate: unify, secure, and modernize their technology stack or risk falling behind. Converging your IT and OT systems isn’t just an upgrade. It’s your ticket to smarter operations, stronger security, and real-time business decisions driven by data.
This section explores why unifying your industrial control systems, OT networks, and analytics platforms is critical to staying agile, scalable, and competitive.
Information Technology (IT)
IT primarily handles data management, business communication, and administrative processes. It includes systems like ERP (Enterprise Resource Planning), MES (Manufacturing Execution Systems), CRM (Customer Relationship Management), and cloud infrastructure. Priorities revolve around data integrity, confidentiality, security, and business continuity.
Operational Technology (OT)
OT focuses on monitoring and controlling physical processes, machinery, and industrial operations. It includes SCADA (Supervisory Control and Data Acquisition) systems, PLCs (Programmable Logic Controllers), distributed control systems (DCS), robotics, and sensors. OT emphasizes uptime, safety, real-time control, and reliability, typically employing proprietary, long-lifecycle hardware with minimal downtime.
Historically, IT and OT operated separately due to their different goals, protocols, security concerns, and staff expertise. However, digital transformation necessitates breaking these silos.
Why IT and OT Convergence Is Imperative Today
Industry 4.0 and Smart Factories
Modern industrial environments are becoming highly connected ecosystems. Integrating operational data from OT networks into information technology systems enables smart factories to make real-time decisions powered by advanced automation, AI, and scalable data analytics. The IIoT forms the digital backbone of this transformation.
Real-Time Data-Driven Decisions
Manufacturing success now hinges on turning real-world operational data from OT devices into actionable insights. By eliminating siloed workflows and manual processes, IT/OT convergence accelerates data analytics, driving intelligent decision-making at every level of business operations.
Competitive Pressures
In a market defined by rapid disruptions, manufacturers must be more agile and responsive. Unified systems give stakeholders visibility across manufacturing processes, reducing lag, improving resilience, and optimizing production with greater precision.
Evolution of Cybersecurity
You can’t ignore OT security anymore. As connectivity increases, so do attack surfaces, especially in industrial control systems (ICS). A unified approach enhances OT cybersecurity, delivering centralized monitoring, stronger threat detection, and seamless integration of IoT security protocols across critical OT environments.
Cost Efficiency
The convergence of IT reduces operational inefficiencies, eliminates redundant tech stacks, and simplifies the management of OT departments. The result: more cost-effective energy use, extended equipment lifecycles, and optimized maintenance workflows tailored to your most urgent use cases.
Benefits of IT/OT Convergence
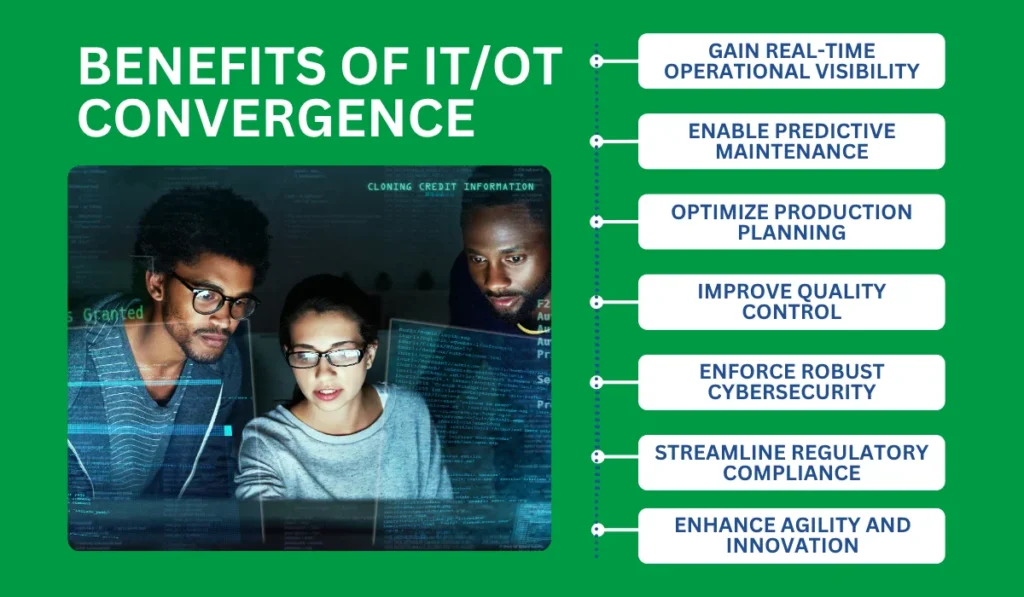
When IT and OT systems converge, the payoff is tangible. Manufacturers can shift from reactive to proactive, from fragmented data to full transparency, and from rigid operations to adaptable, scalable ecosystems. The following benefits highlight why this convergence is a competitive advantage.
1. Gain real-time operational visibility
Integrated IT/OT systems provide unified dashboards, enabling manufacturers to identify bottlenecks, monitor energy use, and track product quality instantly, resulting in immediate, informed decisions.
2. Enable predictive maintenance
Analyzing OT data with IT-driven AI algorithms allows predictive maintenance, significantly reducing downtime, extending equipment lifespan, and achieving considerable cost savings.
3. Optimize production planning
Real-time production data informs ERP/MES systems, dynamically adjusting schedules, reducing waste, optimizing inventory, and enhancing supply chain responsiveness.
4. Improve quality control
Continuous monitoring through converged IT/OT systems helps quickly identify defects, reducing rework and scrap, lowering production costs, and boosting customer satisfaction.
5. Enforce robust cybersecurity
Applying IT security practices to OT environments, including network segmentation and unified SOCs (Security Operations Centers), ensures comprehensive protection from cyber threats, safeguarding industrial operations.
6. Streamline regulatory compliance
Unified data management simplifies adherence to industry-specific regulations and standards, reducing administrative burdens and compliance risks.
7. Enhance agility and innovation
A unified technology strategy facilitates rapid deployment of advanced technologies like digital twins and augmented reality, accelerating product innovation and positioning manufacturers as industry leaders.
Navigating IT/OT Convergence Challenges
Even the most forward-thinking manufacturers face hurdles when merging their IT and OT ecosystems. But each challenge presents a real-world opportunity to strengthen infrastructure, reduce risk, and unlock long-term scalability.
Cultural Divide
IT and OT departments often speak different languages, with IT focused on data security and uptime, and OT driven by production continuity and safety. Bridging this gap requires leadership to invest in cross-training, build integrated teams, and align priorities through shared KPIs and workflows.
Legacy Systems
Many OT devices still operate on outdated protocols not designed for today’s connected environments. Rather than rip and replace, you can modernize incrementally by layering secure gateways, translating protocols, and phasing in upgrades across your industrial control systems (ICS).
Cybersecurity Risks
When OT networks connect to enterprise systems, the attack surface increases. IT/OT convergence must include enhanced OT security measures like segmented network architecture, Industrial DMZs (Demilitarized Zones), granular access controls, and proactive monitoring built specifically for protecting industrial processes.
Data Compatibility and Volume
Disparate data formats and high volumes of operational data can hinder analytics. Standardizing data models, enabling edge computing, and integrating scalable analytics platforms help transform raw OT data into actionable insights across your industrial environment.
Skill Gaps
Few professionals are fluent in both IT and OT domains. Close this gap by investing in internal upskilling, strategically hiring, and partnering with expert providers like Keystone, who understand the technical and operational nuances of convergence.
Keystone: Your Partner for Unified IT/OT Strategies
Successfully navigating IT/OT convergence requires specialized knowledge, strategic planning, and meticulous execution. Keystone possesses deep expertise in both traditional IT systems and the critical nuances of OT environments. We provide:
- Strategic Roadmaps: Custom strategies aligning with your business goals.
- Secure Integration: Robust and secure connectivity solutions.
- Data Enablement: Ensuring seamless, real-time data flows for insightful analytics.
- Industrial Cybersecurity: Comprehensive protection for your critical infrastructure.
- Continuous Optimization: Expert support for ongoing improvement and innovation.
Partnering with Keystone empowers your manufacturing operation to unify technologies, unlock exceptional efficiency, enhance innovation, and secure your future in the era of smart manufacturing.
Conclusion
IT and OT convergence isn’t just about modernization; it’s your competitive edge in a rapidly evolving industrial world. From safeguarding your industrial processes to unlocking the full potential of your IoT devices and ensuring airtight IoT security, a unified technology strategy reshapes how your manufacturing processes operate end to end.
Manufacturers that embrace convergence are optimizing workflows and future-proofing their business, protecting against threats, and enabling smarter, faster decision-making across the enterprise.
Keystone understands the unique challenges of integrating IT with industrial control systems. We help you transform your operations with scalable, secure, and data-driven solutions that deliver real business impact.
Don’t settle for outdated systems or disjointed technology stacks. If you’re ready to streamline your OT environments, protect your assets, and revolutionize your industrial ecosystem, start your convergence journey today.
Ready to unify your factory floor? Schedule your personalized consultation with Keystone now and take the first step toward smarter, more resilient manufacturing.