Nearly 75% of freight in the U.S. moves by truck. But what happens when a disaster brings those trucks to a halt? Your disaster recovery plan is the answer.
In logistics, every second counts—and delays cost more than time. A winter storm, wildfire, or ransomware attack doesn’t just stall deliveries—it can shut down your entire supply chain, damage customer trust, and drain your bottom line. Without a tested recovery plan, you’re gambling with your whole operation.
That’s where disaster recovery comes into play. It’s not just a safety net—it’s a competitive advantage. In this article, you’ll learn how to build a disaster recovery strategy that keeps your operations moving when everything else comes to a halt.
Understanding Disaster Recovery in Logistics
In logistics, disaster recovery involves swiftly restoring essential operations after unpredictable events—from natural disasters like winter storms to IT outages. Since trucks are responsible for most freight movement, disruptions can create bottlenecks that affect your entire supply chain. Being DRP-ready ensures you minimize damage, maintain business continuity, and preserve stakeholder trust.
A robust plan focuses on preparedness. Before catastrophes, you identify vulnerabilities and critical systems, such as inventory management, warehousing, or transportation routes. This assessment anchors your disaster recovery strategy.
Key Components of a Disaster Recovery Plan
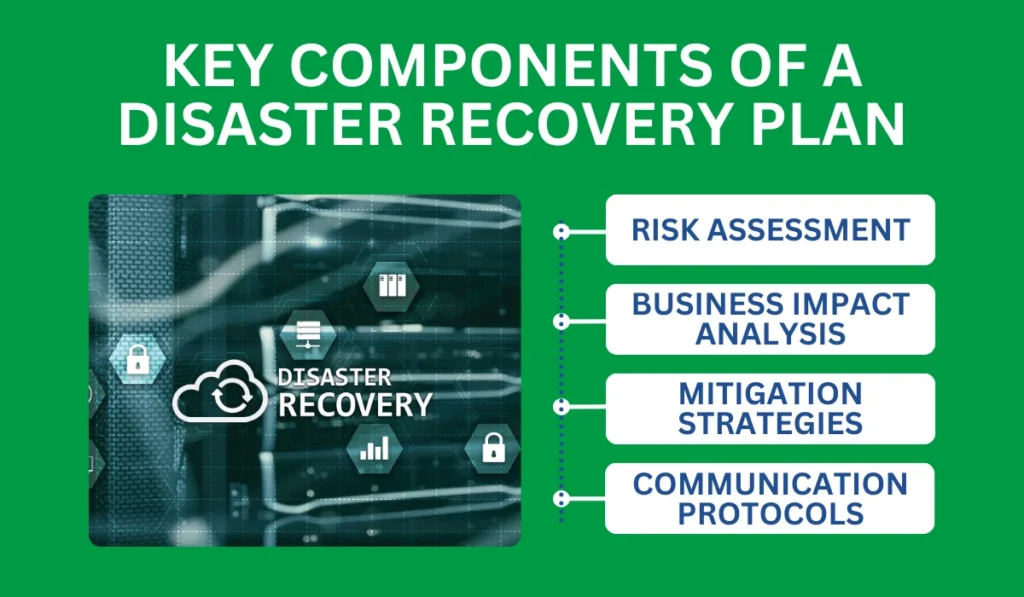
1. Risk Assessment
A thorough risk assessment is essential. By mapping out potential hazards—from wildfires to cyberattacks—your organization gains a comprehensive view of what to prepare for. Businesses with well-defined risk management practices recover more effectively, saving time and money in recovery efforts.
2. Business Impact Analysis
Next, a Business Impact Analysis (BIA) helps you anticipate how disruptions could affect your revenue and operational capacity. For instance, a shortage of raw materials during disaster relief efforts could stall production. By setting clear Recovery Time Objectives (RTOs), you prioritize the order in which you restore critical functions. This ensures your supply chain can resume swiftly, reducing total downtime.
3. Mitigation Strategies
Mitigation strategies include redundant systems, diversified suppliers, and backup warehousing locations. Distributing inventory across locations keeps one disaster from stopping everything. If winter storms close one corridor, alternate transport routes or expedited shipping can keep goods moving to affected areas. Such measures protect you from crippling losses and keep business continuity intact.
4. Communication Protocols
Clear, real-time communication links every part of your disaster recovery framework. Emergency response teams must coordinate with drivers, dispatchers, and providers like managed service firms. Whether you use an internal chat platform or post critical updates on LinkedIn, the goal is consistency and clarity. Team members, partners, and stakeholders should know how to respond when disaster strikes.
Building Resilience into Supply Chains
Redundancy and Flexibility
Your supply chain thrives on flexibility. Redundant paths and distribution centers allow you to reroute around natural disasters or system failures quickly. With alternate carriers or backup logistics, you stay ready when one path fails. This adaptability is the backbone of recovery logistics, letting you maintain service quality even under stress.
Technology Integration
Technology powers fast recovery. Real-time tracking tools, cloud-based backups, and automated alerts enhance risk assessment and reduce human error. These solutions also streamline sourcing, making it easier to handle shortages if primary suppliers fail. In the wake of a disruption, data-driven insights let you pivot quickly, focusing your recovery efforts where they matter most.
Partnerships with Providers
Forming relationships with providers like managed service organizations can strengthen your overall disaster recovery plan. These groups often offer 24/7 monitoring, specialized emergency management tools, and rapid deployment of responders. Aligning their capabilities with yours expands your safety net. You can coordinate with non-profits or public agencies, especially if you need broader disaster relief resources or additional transport options.
Testing and Improving Disaster Recovery Plans
Regular Drills and Simulations
Plans only work if they’re tested. Conduct drills or tabletop exercises regularly to gauge how well team members handle high-stress scenarios like cyberattacks or wildfires. Simulations highlight weaknesses you can fix before they escalate in real life. By reinforcing best practices through training, you cultivate a culture of preparedness and confidence.
Continuous Improvement
After each drill or actual event, analyze what worked and what didn’t. Did alternative shipping routes provide seamless recovery logistics? Were communication protocols effective on LinkedIn or internal channels? Assess performance metrics, gather stakeholder feedback, and update your disaster recovery plan accordingly. This feedback loop keeps your plan agile as threats evolve.
The Role of Business Continuity Plans (BCPs)
DRPs vs. BCPs
A disaster recovery plan focuses on restoring functionality after a crisis, while business continuity plans ensure that operations can continue under crisis conditions. A DRP is your playbook for restoring systems fast.
Integration with Supply Chain Operations
Combining DRPs and BCPs is the surest way to maintain resilience. If a major routing hub is compromised, a well-devised BCP helps you manage sourcing or inventory adjustments until systems are fully restored. By marrying these plans, you create a robust safety net that covers immediate disaster recovery and sustained productivity.
Conclusion: Are You Prepared?
When trucks carry three-quarters of the nation’s freight, the margin for error disappears. One missed delivery can ripple into contract breaches, product shortages, and long-term customer attrition. A solid disaster recovery plan isn’t a nice-to-have—it’s mission-critical.
The logistics companies that win in high-stakes moments are the ones that plan. They assess their risks, build flexible systems, and test them before they are needed. The question is: Will you be one of them?
At Keystone Technology, we don’t just prepare you for disaster—we position you for resilience. With our expertise in risk assessment, real-time visibility, and end-to-end recovery logistics, we help you keep moving when others stall.
Your supply chain’s stability can’t wait. Contact us today and put a real plan in place.