Key Takeaways
- A risk assessment helps find and reduce risks that cause downtime, safety issues, or supply chain disruptions.
- Risk evaluation considers likelihood, financial impact, and failure modes while audits, monitoring, and compliance checks help avoid disruptions.
- AI-driven maintenance, automation, and cybersecurity support manufacturing by preventing equipment failures, cyber threats, and workplace safety risks.
- Data analysis, IT support, and managed services improve decision-making, streamline workflows, and strengthen manufacturing risk management strategies.
What Is a Risk Assessment?
A risk assessment is a systematic process used to identify, evaluate, and mitigate risks in a manufacturing environment. It aims to prevent downtime, safety incidents, and supply chain disruptions by addressing potential hazards before they lead to critical failures.
Here’s how the process works.
Identify Potential Hazards
A checklist for a comprehensive risk assessment process should examine all aspects of the manufacturing environment, including:
- Equipment malfunctions leading to safety risks.
- Human errors that disrupt workflows or cause compliance violations.
- Supply chain risks and disruptions from external suppliers or logistics failures.
Evaluate Operational Risks
Once potential risks are identified, evaluation is crucial. This involves assessing:
- Likelihood and severity of disruptions.
- Financial and safety implications for employees and business operations.
- Failure modes using Failure Modes and Effects Analysis (FMEA) to predict system weaknesses.
Unplanned downtime costs manufacturers an estimated $50 billion per year, highlighting the need for proactive risk mitigation.
Implement Mitigation Strategies
Reducing risks in manufacturing operations requires preventive measures and corrective actions to minimize potential hazards and maintain smooth production. AI-driven predictive maintenance can enhance risk management by detecting malfunctions.
Using AI and IoT sensors, manufacturers can:
- Detect equipment malfunctions before failure.
- Schedule proactive maintenance to reduce downtime.
- Improve production efficiency with real-time monitoring.
Equally important is training stakeholders to recognize risks and follow workplace safety protocols, ensuring that employees can respond effectively to potential issues before they escalate.
Conduct Audits & Monitoring Metrics
Audits help identify weaknesses in workflows, equipment, and safety protocols, allowing businesses to catch potential issues before they cause downtime or compliance violations.
Staying on top of regulatory compliance is equally important. Failing to meet OSHA or industry-specific regulatory requirements can lead to legal penalties and operational setbacks.
Take Corrective Actions & Optimize Workflows
Risk management is an ongoing process that requires continuous improvements. To optimize manufacturing workflows, here are some tips:
- Use data-driven decision-making to refine processes.
- Implement automated monitoring to flag potential risks.
- Regularly update compliance protocols to stay ahead of regulations.
Implementing such strategies enables manufacturers to refine workflows, streamline decision-making, and optimize profitability.
How IT Supports Risk Management in Manufacturing
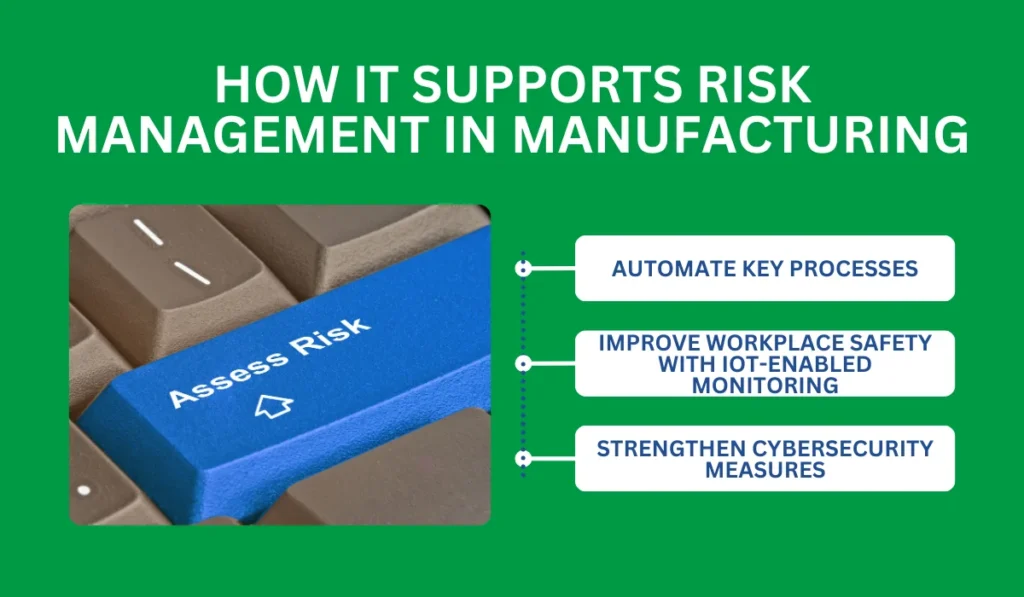
Without a strong IT strategy, manufacturers are vulnerable to supply chain disruptions, cyber threats, and equipment failures.
Here’s how control measures from IT service providers strengthen risk management in manufacturing:
Automate Key Processes
Automation is one of the most effective ways to streamline manufacturing workflows and minimize human errors.
By integrating management systems with predictive maintenance tools, manufacturers can reduce failure modes and anticipate potential impacts before they disrupt production.
Improve Workplace Safety with IoT-Enabled Monitoring
Health and safety risks are a major concern in manufacturing environments.
IT solutions such as wearable technology, smart cameras, and AI-based safety analytics help manufacturers monitor work environments and implement safety measures in real time.
Strengthen Cybersecurity Measures
Cybersecurity is a growing concern for manufacturing facilities. A cyberattack on critical infrastructure can halt production, disrupt the supply chain, and result in significant financial losses.
To prevent such disruptions, IT support can help manufacturing companies strengthen their defenses by:
- Implementing automated security threat detection
- Securing network infrastructure
- Ensuring compliance with regulatory requirements like NIST and ISO cybersecurity standards
Secure Your Manufacturing Processes with Keystone Technology Consultants
At Keystone Technology Consultants, we provide managed IT services tailored to manufacturing operations, including cybersecurity solutions, automation integration, and real-time monitoring to prevent downtime and supply chain disruptions.
Our team also helps with risk assessment templates, compliance audits, and failure mode analysis, so you can stay ahead of potential hazards.
Schedule a consultation with our IT experts today to optimize risk management and safeguard your manufacturing operations.